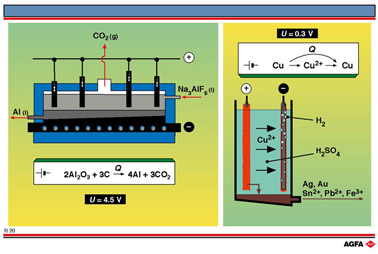
从矿石中精炼一种金属,或将不纯的金属进行提纯时,经常采用电解方法。
1. 金属的电解精炼
在最常见的金属矿石中,金属以氧化物或碳酸盐形式存在。理论上,可以通过电解还原矿石得到金属。不过,实际上更常用廉价的碳或硫进行化学方法还原,这种工艺得到的金属不纯,而且造成环境污染。当对产品纯度要求很高时,电解就是适宜的方法。Al、Co、Cr、Mn、Ta 和 Mg 都是用电解工艺精炼的。
R20以图解方式说明由铝矿石(铝矾土,一种铝的氧化物,含有硅和其他杂质)精炼铝的电解过程。用这种工艺每年生产2500万吨铝。这是仅次于氯气的、最重要的电化学工业产品。汽车、造船、飞机、电子和建筑工业对铝有着巨大的需求。由于铝矾土资源丰富,铝工业的未来十分光明。
1886年,美国人霍尔(Hall)和法国人埃鲁(Héroult)最早开发了由铝矾土电解精炼铝的工艺。1887年,德国人拜耳(Bayer)使之完善。
工艺的第一步是在加压下,将铝矾土溶解在氢氧化钠中,成为铝酸钠。这是一个不涉及电子转移的自发反应。在此过程中,杂质 SiO2和Fe2O3 沉淀出来,

下一步是氧化铝从铝酸钠溶液中沉淀出来。用水稀释后,加入氢氧化铝晶种,或用二氧化碳处理就可完成。分离出沉淀氢氧化铝,加热得到氧化铝,再将氧化铝溶进熔融冰晶石(Na3AlF6)中。
|
|
用生成的电解质熔融盐进行电解,阴极使用石墨材料,阳极为排列成一行的石墨棒。总的电解反应为:

这里 Q 表示消耗的电能。铝在阴极放电,氧气在阳极形成,把石墨阳极氧化为二氧化碳。
相应的半反应方程式为:
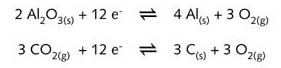
为了使两个半反应的得失电子数平衡,将第二个方程式乘以 3。工艺控制条件为:
- 电压=
= 4.5 V (比较:理论值为2.2 V).
- 电流= 150 kA
- 槽尺寸 = 3 x 8 x 0.7m, 含8个石墨槽(200 小池,每个 15 m3,串联);
- 生产1吨铝需要15 MWh电能,比生产1吨氯气所需电能多5倍。
2. 电解提纯金属
不纯的金属可以通过电解提纯。在电解槽中,用待提纯的粗金属作为阳极,阴极用纯金属。选择控制合适的电极电势,确保待提纯金属非常有选择地在阴极上还原。金属由带正电的不纯金属阳极转移到带负电的阴极上,在此过程中,杂质留在电解液中。
根据要提纯的元素来选择电解液。提纯 Cu、Ag、Au 和 Pt,用水溶液;而提纯 Na、Mg、Ca 和 Al,用熔融盐。
图R20介绍铜的电解提纯。粗铜做阳极,纯铜做阴极,硫酸和硫酸铜的水溶液做电解液。严格控制电极电势,只让铜离子在阴极上还原。
这种方法是提纯铜的最重要方法,每年生产10万吨高纯铜。该法所依据的原理有以下几点:
- Ag、Au和Pt等所有贵金属,电极电势都比铜低,它们不会在阳极上氧化成离子。当铜氧化为铜离子时,阳极瓦解,使得贵金属杂质掉到槽底成为淤泥。
- Sn、Bi和Sb的电极电势比铜高,因此它们在阳极氧化,但是它们的离子与电解液反应,生成不溶性氧化物和氢氧化物,也沉积到槽泥中。
- 铅也氧化,但是形成不溶的PbSO4,沉积到槽泥中。
- Fe、Ni、Co和Sn在阳极氧化,但是仍作为离子留在电解液中。这是由于严格控制电极电势,确保只有铜离子在阴极上还原,其他金属离子需要更高的电极电势才能还原。
从阳极泥中回收贵金属也要使用电解方法。
|